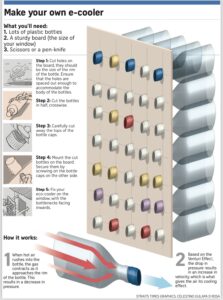
Today we explore a completely passive air conditioner with no moving parts. You may have heard of it. It’s called the Eco-Cooler and it was invented by Ashis Paul, a Bangladeshi innovator.
In 2016, news outlets around the world reported on his creation of a low-cost, electricity-free air conditioner made from recycled plastic bottles. This design aimed to help people in rural Bangladesh cope with the sweltering summer heat, especially those living in homes with limited access to electricity.
The Bernoulli principle and the ideal gas law are the two fundamental principles at play in air conditioners. In theory, an Eco-Cooler functions on the same principles as any compressor driven A/C unit.
The Bernoulli principle states that for an incompressible fluid (like air) flowing in a horizontal stream, an increase in the speed of the fluid is accompanied by a decrease in its pressure. This means as air flows faster, it experiences a drop in pressure. This speed and pressure change is created in the Eco-Cooler as the air stream is forced through the much smaller opening of the bottle neck, causing it to speed up.
The ideal gas law describes the relationship between pressure, volume, and temperature of a gas. According to the ideal gas law, this lower pressure causes the air stream to get hotter by what’s known as adiabatic heating. If this heat can be removed, the air will be chilled upon expansion.
In essence, Bernoulli’s principle creates the pressure differential that drives the heat transfer process in air conditioners, and the ideal gas law explains how this pressure change affects the temperature of the faster moving gas (air in the case of the Eco-Cooler). This interplay of principles is essential for achieving the cooling effect in air conditioners.
I have a treat for you today. I finally took the time to sit down and work out all the engineering behind this simple design.
Here’s what I came up with:
Eco-Cooler, 2L Bottle
Assumptions:
Air speed: v₁ = 2.5 mph (1.12 m/s)
Air pressure: P₁ = 1 atm = 101,325 Pa
Air temp: T₁ = 40°C (313.15°K)
Air density: ρ = 1.225 kg/m³
Specific heat ratio, Cp/Cv: ɣ = 1.4
Given:
D₁ = 4.25” (11 cm)
D₂ = 0.5” (1.27 cm)
Calculate Areas:
A₁ = 𝛑(11/2)² = 95 cm²
A₂ = 𝛑(1.27/2)² = 1.267 cm²
Calculate velocities:
By the continuity formula…
A₁v₁ = A₂v₂
v₁ = 1.12 m/s
v₂ = 95•1.12/1.267 = 84 m/s
Calculate pressures:
ΔP = 0.5 ρ(v₂²-v₁²)
= 0.5•1.225•(84²-1.12²)
= 4,321 Pa
P₁ = 101,325 Pa
P₂ = P₁ + ΔP
P₂ =101,325+4,321 =105,646 Pa
P₂/P₁ = 1.043
Calculate Temperatures:
T₂ = T₁ (P₂/P₁)^((ɣ-1)/ɣ)
= 313.15•(1.043)^(0.4/1.4)
= 316.9°K
= 43.8°C
(As a result of radiative cooling)
T₂ => 313.15°K
After expansion
T₃ = T₂ (P₁/P₂)^((ɣ-1)/ɣ)
= 313.15•(1/1.043)^(0.4/1.4)
= 309.4°K
= 36.3°C
= 97.34°F (down from 104°F)
And there you have it ladies and gentlemen. This is how the Eco-Cooler is supposed to work. However…
The Eco-Cooler, while innovative in its concept of a passive cooling solution, has a mixed reputation. You will find lots of YouTube video reviews online and virtually every one of them claims that it doesn’t work.
I think it’s clear why. In the design, as described, there is literally no means by which to remove the excess heat energy. You must cool the compressed air before allowing it to expand again if you want satisfactory results. Isn’t that how your standard compressor operated A/C unit works? Of course it is.
The faster moving air at the outlet may help increase evaporative cooling effects but that wasn’t the purpose for its compression in this design. It makes absolutely no sense to immediately allow the hot air to re-expand without having removed excess heat energy from it first.
The addition of heat radiating fins to a pipe of increased length would give this thing a fighting chance. The longer path would provide additional time to carry out the heat transfer. In extreme cases it may even be necessary to use a water bath to carry off that excess heat. Yes, this would add expense and complexity but the dividends in performance should be well worth it.
Eco-Cooler Summary
So, to summarize then,
Pros
Low Cost and Simple Design: Made from recycled materials like plastic bottles, the eco-cooler is very inexpensive to build. It doesn’t require electricity, making it suitable for off-grid locations.
Passive Cooling: The design utilizes the Bernoulli principle for a passive cooling effect, offering an alternative to energy-intensive air conditioners.
Environmental Benefits: By using recycled materials and avoiding electricity, the eco-cooler has potential environmental benefits.
Cons
Limited Cooling Capacity: In its basic form, the eco-cooler’s cooling effect is relatively weak and may not be sufficient for significant temperature reduction, especially in hot climates.
Real-World Limitations: Factors like friction and imperfect heat transfer can hinder the effectiveness of the cooling process.
Need for Improvement: The basic design requires modifications like pre-cooling with radiator fins to achieve a more noticeable cooling effect.